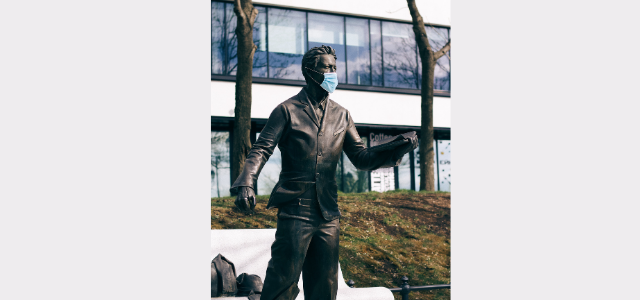
Office Metamorphosis from Physical to Virtual
John Seabrook has written an insightful article, published by the New Yorker, about the paradigm shift from physical offices to remote work and how companies may navigate these unchartered waters in the wake of the pandemic.
The writer poses a thought-provoking set of questions: “What’s an office for? Is it a place for newbies to learn from experienced colleagues? A way for bosses to oversee shirkers? A platform for collaboration? A source of friends and social life? A respite from the family? A reason to leave the house? It turns out that work, which is what the office was supposed to be for, is possible to do from somewhere else”.
In the digital world before the covid shift, the tools that were meant to improve communications in the workplace actually reduced the in person interactions that the open-plan office was supposed to enhance. Now the same tools make it possible to work remotely rather than wasting time online in the office. Surveys cited in the article show that employees actually worked harder from home during lockdown.
Expensive office space in prime markets has become a costly burden. The office has gradually evolved from high-to-low to no workstation panels, culminating in rows of desking systems. That proximity won’t do in the era of the pandemic. Conventional wisdom further evolved during the pandemic, championing the use of antimicrobial materials for high touch locations in the workplace and installation of plexiglass shields and signage promoting social distancing. Finally it became evident that the virus was more likely to spread through HVAC systems than through surface contact and that plexiglass would not slow the spread if the virus is circulating through the ventilation systems.
A VP at Microsoft interviewed by the writer explained that the pandemic is creating a “second digital transformation” by connecting employees’ computers through the cloud wherever they are working. Companies are investing money saved by downsizing physical offices, into cloud-based offices with digital whiteboards and virtual conferencing tools. One of the writer’s ironic conclusions is that the virtual office may eliminate privacy altogether, as every keystroke will be trackable.
Read the full article at:
https://www.newyorker.com/magazine/2021/02/01/has-the-pandemic-transformed-the-office-forever
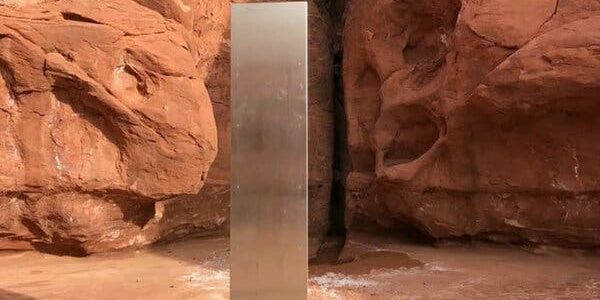
Helicopter Survey of Sheep Spots a Strange Steel Monolith Embedded in Barely Accessible Rock in the Desert
Speculations abound about how the Sci-Fi invoking 12’ monolith was transported and installed in the forbidding terrain. As specialists in transporting equipment to challenging remote locations, we believe that the mysterious 3-sided monolith and the rock cutting equipment had to be transported by helicopter or a purpose-built all-terrain vehicle in order to access the inhospitable terrain.
According to Lt. Nick Street, a spokesman for the Department of Public Safety, the authorities were confident that “it’s somebody’s art installation, or an attempt at that.” As to how it was transported to a remote spot in Red Rock Country, he said, “Somebody took the time to use some type of concrete-cutting tool or something to really dig down, almost in the exact shape of the object, and embed it really well. It’s odd…There are roads close by, but to haul the materials to cut into the rock, and haul the metal, which is taller than 12 feet in sections — to do all that in that remote spot is definitely interesting.”
Read more about this mystery at:
https://www.nytimes.com/2020/11/24/us/Utah-monolith-red-rock-country.html
(Credit: Utah Department of Public Safety)
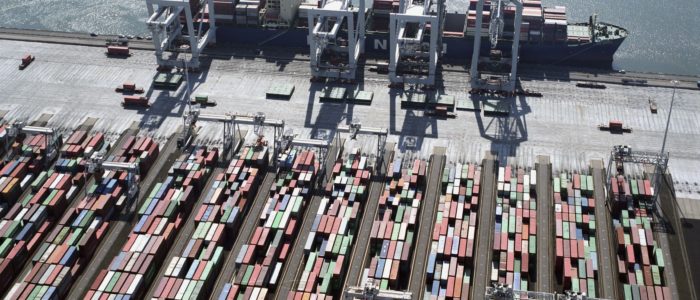
Critical Cargo Bypassing Bottleneck at Ocean Ports Aboard Chartered Passenger Aircraft
Bottlenecks in the global supply chain are being bypassed by repurposing passenger aircraft for critical cargo. With retailers worldwide closing shop, warehouses becoming backed up with undelivered goods, increasing trucking restrictions and driver shortages, importers are being forced to delay delivery of goods that can’t be sold or stored. This clogs ports with containers and slows critical food and medical supply chains. Ocean carriers are rerouting containers to transshipment ports and yards close to destination so they can reach markets more quickly when business resumes, while keeping major ports unclogged. To keep food and medical supply chains flowing, critical cargo is moving on passenger aircrafts that have been idle since the travel ban.
Read more about how the ocean and air transport industries are adapting to the crisis at:
https://www.joc.com/air-cargo/idle-passenger-planes-take-mini-freighter-roles_20200317.html
(Photo credit: IAPH/International Association of Ports and Harbors)
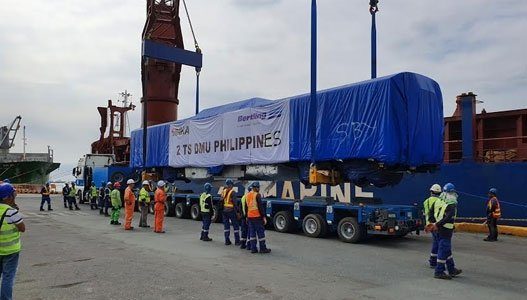
Journey of a Typical Railcar from Factory Through Locomotion in Another Country
The international journey of new railcars from factory through installation on a track overseas, is not as simple as booking trailers, a ship and cranes.
It starts with engineering modifications to the railcars to create lifting beams and lashing rings. COG calculations are made to ensure the lifting plan keeps the railcar balanced through the lifting operation. At the same time, early shipments are dispatched with tracks, welding equipment and materials, communication and signal systems, depot structures and fixtures as well as track maintenance equipment.
A local crew starts installing the tracks and associated equipment at destination while the railcars are being built and custom fitted with lifting and lashing points for the journey.
This complex process is designed and managed by specialists like Overseas Brokers, with the help of marine engineers who assist in creating lifting diagrams noting center of gravity, drafting of required crane spreader specifications, making angle and clearance calculations, as well as oversight by marine insurance surveyors who supervise every step of the loading/unloading, lashing, lifting, delivery and placement on the final track at destination.
Note: The lifting configuration of the railcar in the photo is designed to maintain a 90 degree angle and keep the railcar level when lifted, to prevent the lifting cables from causing damage to the side panels of the railcar.
Read more about such projects at:
(Photo Credit – above: Via The STAT Trade Times: “This shipment is the first delivery of PNR trains and seven more new trainsets are set to arrive in 2020.”)
https://www.topgear.com.ph/news/motoring-news/pnr-indonesia-train-coaches-a4354-20191211
(Photo credit: DOTR – via TopGear)
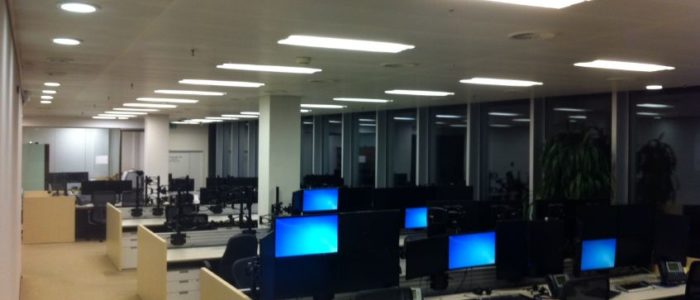
Lacour Trading Desks Installed in Geneva
Take a look at a project we completed in Geneva, Switzerland consisting of trading desks manufactured by LaCour in the US, and exported on behalf of Insidesource, a major contract furniture dealer.
Product was loaded in a container in NJ, shipped to Rotterdam and trucked to Geneva where we cleared customs, delivered and installed by our local logistics partner.
The same process was duplicated globally for this trading company’s worldwide offices.
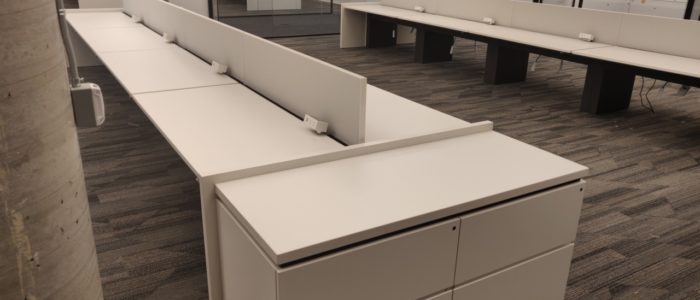
Innovant Partners With Overseas Brokers For Large Trading Desk Project In Montreal
We provide global logistics solutions for the contract furniture industry
Here’s just one example: A 600 desk project we handed in Montreal for a top tier global financial services firm. These are height adjustable desks, made in the US by Innovant, a leading manufacturer of trading desks, benching, private offices and conference room furniture.
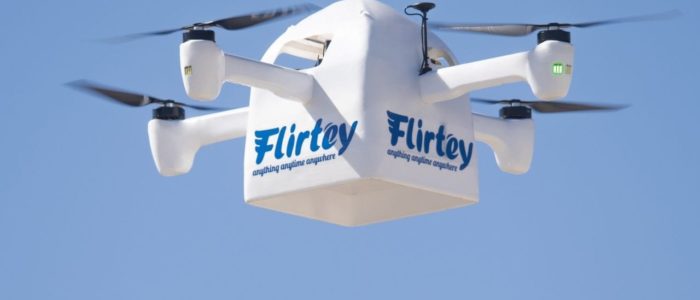
A Drone Delivery Startup Aims To Provide 10 Minute Package Delivery Services
Flirtey has partnered with Dominos and 7-Eleven to test a delivery method that could replace the hub & spoke model used by most logistics providers. Hub & spoke deliveries are typically routed via distribution centers. Drone delivery enables vendors to deliver directly from the nearest store to your door. Flirtey has even partnered with an ambulance service to deliver defibrillators to people suffering a heart attack before paramedics arrive. Read more about this paradigm shift here.
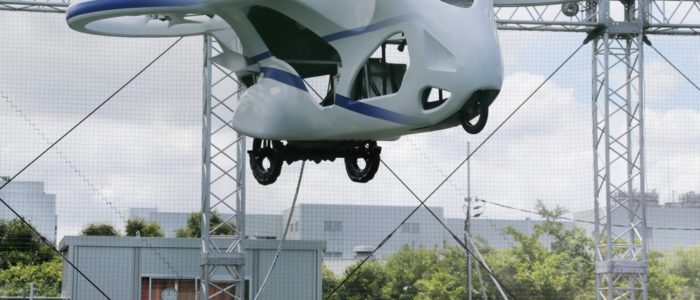
Are Drone-Like Flying Cars the Future of Package Delivery and Short Range Passenger Transport?
NEC of Japan has tested a prototype of an EVtol aircraft (electric vertical takeoff and landing). The Japanese government intends to develop driverless aircraft for people by the 2030’s, while Uber Air is reportedly developing a VTOL aircraft (vertical takeoff and landing aircraft) for demo flights in 2020 and commercial flights in 2023 in Dallas, Los Angeles and Melbourne. Read more here.
(Photo credit: AP Photo/Koji Sasahara)
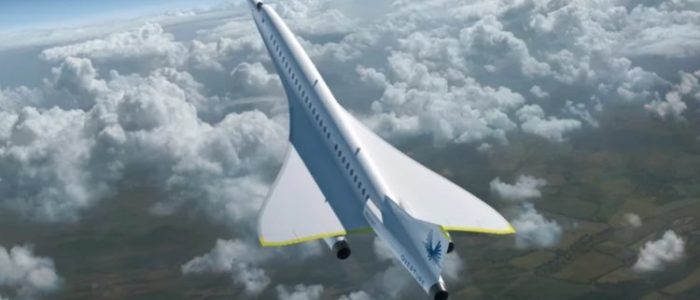
The Future Of Environmentally Sustainable Supersonic Air Travel And Time-Critical Air Freight Is At Our Doorstep
Boom Technology, a US-based supersonic transport startup, is developing a supersonic jet in partnership with Japan Airlines that will fly from NY to London in less than 3.5 hours. The new jet, named Overture, is expected to be in service for passenger flights as soon as 2025-2027. The reappearance of supersonic jets has the potential to transform the marketplace for time-critical air freight carriers and for courier giants such as Fedex and DHL, by reducing the transit time as well as the environmental impact of freighter aircraft. Boom Technology is exploring ways to improve on the Concord jet by using a new technology being developed by Prometheus, for producing aviation fuel which is converted from CO2 emissions in the atmosphere into liquid hydrocarbon and then transformed into aviation fuel. As a result of developments in propulsion technologies, the new jet is expected to fly at speeds in excess of Mach 2.2 without the use of afterburners, reducing the noise level and environmental damage associated with the first generation of supersonic aviation. Read more about this exciting development here.
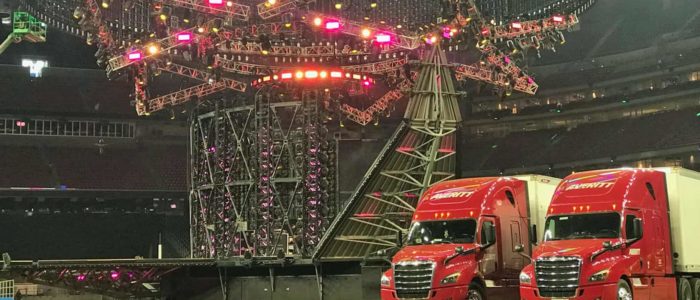
Managing The Logistics Of Rock And Roll Concert Tours Leaves No Margin For Error
Concert tours require meticulous planning, reliable carriers, knowledge of international customs requirements, 24/7 attention to detail and lots of care. Large tours with back to back gigs maintain at least 2 identical sets of equipment which leap frog between venues to allow time for one set to be loaded in and erected, while the previous set is being taken down and loaded out for the next venue. Read more about challenges unique to the touring entertainment industry here.